Difficult Flooring Problems…We Can HELP!
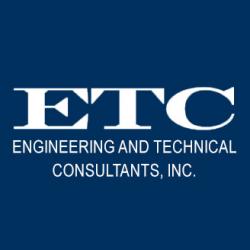
Buckled wood flooring, moldy carpets, peeling sheet flooring, and bubbles in liquid applied floors can all be signs of excessive or trapped moisture below the floor covering. Moisture permeating from concrete floor slabs affects the performance of flooring systems such as resilient and textile floor coverings and coatings, and can cause floor covering system failures such as, debonding and deterioration of finish flooring and coatings, as well as microbial growth. Manufacturers of such floor covering systems generally require moisture testing to be performed before installation on concrete. Omitting these tests when they are required by the Manufacturer may void the flooring system warranty. This is a relevant issue for new construction or any project where the flooring/coating manufacturer requires ASTM testing prior to the flooring installation.
All of the concrete slab moisture tests require proper surface preparation (removal of adhesives, previous coatings, surface impurities, etc.), followed by a waiting period (usually 72 hours) under typical ambient conditions. Three tests are required for the first 1,000 square feet of floor space, and one additional test is required for each additional 1,000 square feet. When the test results are compared to the flooring manufacturer’s installation requirements, they can indicate if the concrete slab is acceptable for the installation of resilient flooring.
Four different tests can be run on concrete slabs to check the moisture content. The ASTM F710 standard test method involves the measurement of the pH level of the concrete surface, which is required data for all three of the slab moisture testing methods. As Portland cement hydrates, calcium hydroxide and other alkaline hydroxides are formed. The pH of wet concrete is extremely alkaline, while the pH of a floor with at least a thin layer of carbonation is typically between 8 and 10.
ASTM F1869 measures the Moisture Vapor Emission Rate (MVER) of a concrete slab expressed in lbs/1000 ft2/24 hours. This is achieved by placing a dish of calcium chloride on the slab surface under a plastic cover, allowing the crystals to absorb moisture emitted from the slab over a 72 hour period, and weighing the dish after. Typically, flooring manufacturers require an MVER of 3 lbs/1000 ft2/24 hours or less before installation.
ASTM F2170 measures the relative humidity throughout the depth of the concrete slab as a percentage by drilling a small diameter hole into the slab. ASTM F2420 is another test that also measures the relative humidity of the slab as a percentage, but this uses an insulated hood positioned over a portion of the concrete slab. This method simulates the placement of resilient flooring on the concrete surface itself, but it is not commonly used in the United States.
So how long does it take for a concrete slab to dry out, and how soon should the slab moisture tests be performed? Unfortunately, the drying time for concrete slabs can vary greatly depending on atmospheric conditions and the mix design. However, a typical 4” thick slab with a water-cement ratio of 0.45 can take anywhere from 90 to 120 days to achieve an acceptable range. Slabs that contain lightweight aggregate or that only dry from one side (such as slabs installed over a moisture vapor retarder or on metal decking) may need a much longer drying time.
If the concrete slab does not meet the flooring manufacturer’s requirements for installation, it is advisable to wait at least 30 days before performing another set of tests. In the interim, you can perform a plastic sheet test per ASTM D4263 (commonly called a mat test), and if the slab appears dry, then a re-test using the more rigorous ASTM procedures, above, can be performed.
Please give us a call if you are experiencing flooring problems. We have a certified technician ready to help!!