Strengthening Concrete with Fibers
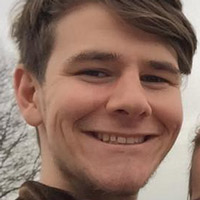
Fiber-reinforced polymer or FRP, is a concrete repair material that has been growing in popularity in the United States for close to 25 years now. FRP, as its name implies, is a polymer material with carbon, glass or steel wires imbedded in a polymer resin. The question is what is it good for? Often, concrete structural elements – slabs, beams, or columns, – that compose a building, will occasionally need to be strengthened due to a change in usage or loading. The typical remediation for such conditions includes the installation of structural steel frames and other elements, to provide additional strength support for the existing concrete. However, FRP is an alternative that is able to provide strengthening effects, with much lower weight. FRP can be applied to the surface of the element to provide support, via two methods. In both methods careful attention to proper surface preparation must be taken, including a primer coating to penetrate the substrate and enhance bonding ability. In some cases, an epoxy putty application is applied to create a more even bonding surface.
- FRP fabric can be applied on site by combining the fibers and liquid polymer resin, and utilizing a wet lay-up process.
- They can also be pre-manufactured off site and arrive as bars, plates, and rods and glued to a structure.
After application, the FRP becomes an integral part of the structural element providing both flexural and shear strengthening, or column confinement and ductility. The increase in structural capacity from FRP is due to the ability of the resin to transfer loads to the fibers, and the fiber’s large capacity to carry tensile loads, varying from 2-5 times the capacity of steel. So why FRP? Despite having a higher material cost than traditional strengthening methods, the reduced installation time, equipment utilization and labor can offset the higher material cost especially in areas with limited access, which would explain the increased usage of FRP over traditional methods.