Blog
View All Blog Postings
Hammering Out Concrete Problems
If you have a concern about the integrity of cracked or spalled concrete, consider using a simple but reliable test.
Tap the concrete with a hammer. A sharp, ringing sound tends to indicate that the concrete is sound. A dull hollow sound means that the concrete may be unsound, unbonded, delaminated or deteriorated.
It sounds simple and it is…….hammer away!
Check Out Our New Digs
What’s so great about Philadelphia? Let’s see….Liberty Bell, Museum of Art, ETC, Penn’s Landing, ETC, Philly Cheese Steak, Eagles, Rocky Statue, ETC, Shopping, Fine Dining, ETC, Battlefields, History, ETC, Brotherly Love, Olde City, ETC, Philly Pretzels, ETC, Independence Hall, ETC, Drexel, Philly Fanatic, ETC, Temple, Flyers and….
We are pleased to announce our new office in Bala Cynwyd, Pennsylvania
Send me an email mindy@etc-web.com of YOUR favorite thing about Philly. Be sure to include your address. Person with the best answer wins a prize!
Just Breathe
Installing linoleum or similar covering directly on concrete floors can be problematic if there is moisture in the slab. This is especially a concern with on grade slabs where there may be moisture under the slab that can permeate upward. Linoleum and similar floor coverings act as a barrier that can cause moisture to be trapped under the flooring. When this happens, the floor covering can unbond, warp and become a serious hazard.
Carpet covering will let moisture vapor pass through and normally are not a problem. Carpet can be a solution where other floor coverings are adversely affected by moisture.
If a linoleum or similar covering needs to be installed, it is important to understand and analyze the moisture present in and/or under the slab. Various types of moisture testing can be performed to help verify that the concrete is dry enough to allow the installation of an impermeable floor covering.
That A Boy!!
It is with great pride that we announce that Luke Valentine has been accepted into the University of Maryland Graduate School to study Structural Engineering, which is ranked in the top 25 of all Civil Engineering Graduate Schools in the nation. Luke is our longest tenured intern having been with us for almost two years. In that time he has been able to balance his studies while gaining practical engineering experience by working part time during the school semesters and full time during his breaks. The next year will likely fly by as he graduates with his Bachelor’s Degree in May and continues straight into graduate studies. We wish him well as he pursues a Masters Degree.
So if you see Luke on one of your ETC projects…shake his hand, give his a pat the back or say “WAY TO GO”! It’s well deserved!
Permit Delays – Please Read!
We have currently experienced a new trend with several of the local jurisdictions within the DC Metropolitan Region with regard to the time frame it takes to obtain a building permit for rehabilitation projects. In the past, it was assumed that permits would be reviewed, approved and released within 2 to 4 weeks. Just recently, we have been told by the permit offices that it could take anywhere from 9 to 16 weeks to obtain the permits due to downsizing of their departments. Based on this information, we recommend that Owners be aware of this issue and plan accordingly as to not delay the start of upcoming projects if permits are required.
Thanks Big Joe!
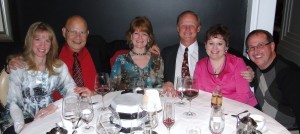
There’s no host more gracious than Joe Shuffleton and his latest dinner outing proved to be no exception! From the fine dining to the excellent company, it was an evening to relish. Thank you for including ME among your ELITE group (Steve & Sandy Wright, Tom & Susan Hickerson and Joe Shuffleton)! Whether in the trenches of business together or enjoying a lovely glass of wine, this is one top-notice group of people! (and boy do they know how to have FUN!! )
Using Sacrificial Zinc Anodes to Inhibit Corrosion
When repairing concrete damage caused by embedded steel corrosion, it may not be enough to simply remove and replace. In applications where the existing steel, after being cleaned and coated, will come into contact with both old concrete and new patch material, accelerated corrosion is possible due to the differences in electrical potential between the old and new materials. To prevent corrosion, zinc anodes can be installed prior to new concrete placement. The zinc, which has a higher corrosion potential than steel, will corrode in preference to the more noble metal, steel.
Associa Cares
We were delighted to be involved with the Legum & Norman educational update & mini-expo in Rehobth Beach, DE this past week. Mr. Chad Toms of Whiteford Taylor Preston, LLC conducted a very informative presentation on the Delaware Uniform Common Interest Ownership Act (DUCIOA). I’m sure his office in Wilmington, DE would be pleased to assist you with any legal concerns or questions you may have.
Thank you to Patty Dubuque, Erika Grden and all those at Legum & Norman for the work you to do to service our communities. Electing to donate all the proceeds from this event to Associa Cares was greatly appreciated. For those of you that are not familar with this non-profit organization, all donations go to help communites in need as a result of natural or man-made disasters. Through the work of these wonderful volunteers, Associa Cares is able to help many communites all across America! Keep up the great work Legum & Norman and thanks for letting ETC be a small part of it.
Donations to Associa Cares can be made by visiting www.assicacares.com and clicking on “Donate Now”
Extreme Makeover!
Parking garage rehabilitation projects can take a while to complete, but the payoff can be huge especially when the aesthetics are improved as shown. This recently completed garage is a prime example of a dark, unsafe looking, cavern-like parking area that was transformed into a bright space. New lighting, painted columns and ceilings, and a protective waterproof driving surface have transformed the aesthetics of this garage.
The waterproof membrane will protect the investment made in structural concrete repairs for years to come by preventing water from entering the concrete and corroding the embedded steel reinforcement. Leaks between slabs have also been addressed, which will stop mineral deposits from dripping onto cars in the level below and ruining the painted finish.
No Need to Whine!
It was so NICE seeing many of you in Washington, DC this past weekend at the CAI Conference & Expo! We enjoyed the chance to reminisce with past clients, discuss issues with current clients and look forward to opportunities with future clients.
It was a true pleasure seeing everyone and thank you for stopping by to say hello!
While we were able to assist many attendees with their building concerns on Saturday, it was also great to enjoy a little fun with the ETC wine hunt. No need to whine…if you weren’t able to find your match to WIN a bottle of wine, you will have another chance in April! Please come by and visit our booth at the Property Management Association Expo on April 14th at the Prince Georges Sports Complex in Landover, Maryland. We hope everyone is a winner this time! Nothing says happiness like wine and engineering, but of course NOT TOGETHER…we engineer responsibly! Look forward to seeing you next month!
Come By And Say Hello
ETC and the Washington Metropolitan Chapter Community Associations Institute (WMCCAI) invites you to attend the largest community association industry event in the Washington metropolitan area on March 12, 2011, at the Washington Convention Center. ETC is in booth #211, so please stop by and say hello! Professional engineers on site to answer all your building questions.
The 2011 WMCCAI Conference & Expo will feature 15 educational sessions on pertinent topics that affect those who live in and work with community associations. Approximately 190 companies and organizations will be on the exhibit hall floor showcasing goods and services of interest to community associations. Hope to see you there!
Where The Sidewalk Ends
Now that the snow is starting to melt away, we have started to find heaved (raised) sections of concrete sidewalk due to the cold weather which present a potential trip hazard. As a general rule, a ½”or more difference in the level of the walking surface can be a potential trip hazard. We have also seen damaged concrete sections from freeze/thaw action. It seems that the winter has been tough on concrete this year and an inspection of your property is advisable so that timely repairs can be made.